
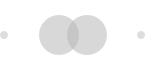
导言:精益生产的崛起
丰田汽车在1950年考察美国大规模生产方式后,认为这种方式到处充满“浪费”,在资源匮乏的日本根本行不通,因此自行摸索发展新的生产方式。丰田汽车从消除“浪费”开始,进行各类以改进为核心的工艺改善活动,逐渐形成独树一帜的生产方式,西方学者称之为“精益生产方式”(Lean Production System)。美国麻省理工学院耗时5年,对世界14个国家的汽车产业进行研究后认为,精益生产方式在应对多样少量的产品时,不仅不会增加成本,交期也能大幅缩短,往往能够在当前激烈竞争的市场中脱颖而出。
精益生产方式、精益管理就是经过《改变世界的机器》和《精益思想》的作者,当时美国麻省理工学院的研究员——詹姆斯·P·沃麦克(James P.Womack),丹尼尔·T·琼斯(Daniel T. Jones)的分析和总结所发展而成的理论概念,后来被广泛应用于其他制造业和服务业。

丹尼尔·T·琼斯(Daniel T. Jones)接受了2021年ILSSI终身杰出贡献奖,他分享了对精益管理的深入思考。琼斯在ILSSI的国际研讨会上解释了精益管理的演变历程,强调精益不仅仅是关于工具和技术,而是一种不断学习和提高能力的过程,需要创建一个有效的管理体系,包括基础稳定、流程改进和问题解决,以及对管理层的重要作用。最后,琼斯指出,精益的真正价值在于能力的提升,帮助组织更好地应对未来的挑战。
相较于大规模生产方式倾向于强调设备效率,力求排除人为变因,追求个别工艺的优化,精益生产方式则重视强化人员的作业效率,追求人与设备的协调,以整体生产流程为考虑焦点。大规模生产方式往往利用专用设备进行大批量生产,并对单一工艺进行改善,以降低单位生产成本,同时也通过庞大的生产量来获取规模经济,平衡换模时的损失。精益生产却以缩短换模时间为减少人员浪费的基础,配合小型通用设备提升生产弹性;并致力于减少人员作业的浪费,以互助的作业方式平衡生产,使整条生产线的效率最佳化。
此外,在充分发挥每一位从业人员能力的理念下,精益生产通过OJT(在职培训)的方式,在工作场所通过实际操作培训具备多种技能的员工,赋予员工更多的决策权,并在重视团队互动合作的基础上完成工作任务。对于供应商或客户,精益生产也秉持平等尊重的态度,建立长期稳定的关系,以实现紧密整合所有产品流程的目标。同时,为了能够依市场需求生产出适时适量的高质量和多样化产品,精益生产对如何缩短产品从研发到生产、销售的时间,建立产品差异化优势,给予高度重视。
1990年前后,精益生产开始从日本普及至全球,2000年美国信息科技创新泡沫化之后,成为全球生产系统的显学,在众多行业中取代了大规模生产方式。不少欧美企业面对环境变化带来的生存危机,采用精益生产后起死回生,再创佳绩。尤其在2010年的“世界工厂”中国大陆,精益系统的实践程度直接反映了工厂的盈利能力;面对中国大陆的竞争,精益系统变革也成为台湾企业升级与转型的核心能力。
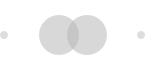
产业升级与国际分工
回顾汽车工业的发展历史(见下图),19世纪末的手工生产时代,依靠师徒制或少数人生产的车辆种类繁多,产量极为有限,这可以视为欧洲高级车生产模式的基础。1914年是福特T型车的全盛期,创造了年产量200万台的空前纪录,追求规模化的大规模生产方式逐渐以横扫之势席卷全球汽车工业,其他行业也纷纷效仿以提升竞争力。然而,随着大规模生产方式的式微,70年代起以丰田式生产为代表的日本精益生产体系逐渐崛起,在全球石油危机的阴影下屹立不倒,丰田汽车甚至因此在2008年攀登全球顶峰。

生产模式的变迁并非汽车产业的专利,鞋类、家电、相机、服饰、笔记本电脑、工具机等行业亦有类似之处。从国际生产动向来看,结合不同环境的优势,采用最佳的生产模式,已成为制造策略的指标。义大利高端鞋类和法国巴黎服饰追求产品独创性,尊重“工匠精神”,展现了手工生产的特色与优势;而中国大陆凭借成本优势,成为世界运动鞋或廉价成衣生产基地,利用大规模生产模式获得了最大市场效益;追求产业升级的台湾和日本则在不同程度的多样少量生产市场和质量定位中取得了生存的立足点。
2010年前后,刘仁杰教授在日本神户大学、大阪市立大学做客座期间的系列考察中发现,日本笔记本电脑巨头Panasonic、服饰品牌优衣库(Uniqlo)、台湾自行车A-Team联盟、全球空调巨头大金(Daikin)、钣金机械领军企业Amada、相机巨头佳能(Canon)、代工王国鸿海科技集团与宝成国际集团,均以精益系统的实践为发展根基。日本、台湾与中国大陆在精益系统的实践上持续引领全球。
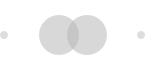
选择符合市场环境的生产方式
事实上,手工生产、大规模生产与精益生产不存在何者最佳的问题,而是各有其重视的核心要素与适用的市场环境。手工生产重视产品创意,通过精致高端化提升产品附加值,客户范围相当有限;大规模生产则通过前期预测,依靠幕僚群的规划控制生产活动,重视效率管理,以成本优势进入消费市场。精益生产方式以客户和改进为核心,按客户需求灵活调整生产系统,追求速度、质量及差异化竞争优势。
然而,随着科技进步和社会日益富裕,人们越来越追求个性化发展,P、Q、C、D、S成为影响生产方式的重要要素。所谓P是指产品(Product),即顾客希望的多样化产品;Q是质量(Quality),即优良可靠的质量;C是成本(Cost),即顾客能接受的产品价格;D是交期(Delivery),即快速将最好的产品交付给顾客;S是安全(Safety),即产品使用的安全性。能够同时符合PQCDS五要素的生产方式,逐渐成为现代企业的生存基础。而至今似乎只有精益生产具有足够的优势能够长期应对这一趋势,手工生产和大规模生产的应用空间则日渐缩小。
当大规模生产在当今环境中面临诸多瓶颈时,企业往往直觉性地通过自动化或信息化来克服障碍,耗费资金购买最新的设备或信息系统,但结果往往难有起色。充分授权、利润中心及组织扁平化等也被认为是大规模生产思维下的解决良方,但常导致部门间摩擦或产生新的纠纷,而通过裁员实现组织精简化也仅能带来短期效果。迎接精益系统革命的挑战,联合从业人员和供应商共同强化生产体制,或许才是唯一的最佳途径。