从零开始,中国高铁用了短短十几年的时间便实现了从追赶到引领的跨越,建设了全球最长的高铁网络,超过4万公里的运营里程连接了全国的大中城市。
尽管如此,当我们骄傲地谈论中国高铁国产化率高达97%时,不禁会问:那剩下的3%又是什么呢?而未来,我们是否有望实现真正的100%国产化?

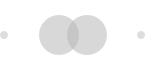
从无到有:中国高铁的自我超越之路
中国高铁的发展历程可以用“从无到有,从追赶到引领”来形容。这段旅程不仅展示了中国在科技和工业领域的快速进步,也见证了一个国家在基础设施建设上实现自我超越的决心和智慧。
1978年改革开放元年,邓小平便敏锐的察觉了高铁铁路发展的重要性,并借助夸赞日本新干线的建设,发出了“我们必将迎头赶上”的呼喊。

90年代初,京沪铁路规划的报告起草完成,中国高铁就此发车。2004年,中国政府正式启动了《中长期铁路网规划》,决定引进国外先进技术,并通过合作与自主创新相结合的方式,发展高速铁路。
在初期,中国主要与日本、德国和法国等国家的企业合作,通过技术引进、联合设计和制造等方式积累经验。

例如,北京至天津的京津城际铁路,便是中国高铁项目的早期试点之一。该项目引进了日本川崎重工的技术,并在国内实现了部分自主化生产。
通过早期项目的成功实施,中国逐渐积累了高铁建设和运营的经验,并开始在全国范围内大规模推广。

2008年,伴随着北京奥运会的召开,京津城际铁路正式开通运营,成为中国第一条具有国际先进水平的高速铁路。这条线路的成功运行,标志着中国高铁迈出了关键一步。
进入21世纪,中国高铁进入了全面自主创新和全球引领的新阶段。以“复兴号”为代表的新一代高速列车,完全由中国自主研发制造,标志着中国高铁技术达到了世界领先水平。

“复兴号”不仅速度更快,最高运营速度可达350公里/小时,而且在节能环保、智能化和乘客舒适度方面也有了显著提升。
如今,建设铁路对于中国来说早已不再是需要求助“洋大人”的时代,甚至曾经的日不落英国都要请我们去修铁路,可见我国的高铁逆袭之路已全面完成。

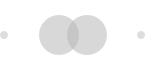
为何 '高铁之骨'仍依赖进口?
根据最新的数据显示,我国的高铁国产化已高达97%,这个数字听起来已经是十分傲人的成绩了,但这“缺了角”的数字看起来总是让人有点别扭,有人就会问了,剩下的这3%究竟是何等高科技,为何我国还无法自主生产?这关键的一个零件便是高铁轴承。
当我们谈到“高铁轴承”,可能会觉得有些陌生,高铁轴承是高速列车中的关键零部件,就像高铁的“骨架”一样。它们的作用类似于人体的关节,连接不同部分并允许它们相对旋转。

这些小小的零件承担着巨大的责任。高铁运行速度快、载荷大、温度变化大,而轴承需要在这些极端条件下保持稳定。如果轴承出现问题,高铁可能会出现安全隐患。

正因为如此,高铁轴承的制造工艺也是十分严苛,高铁轴承的公差范围通常在0.001毫米。为了比较这个数值,人的头发直径大约为50至70微米,这意味着高铁轴承的制造精度要比一根头发细数十倍甚至数百倍。
高铁轴承的内圈和外圈的圆度误差必须控制在1微米以内。这意味着如果将高铁轴承的内圈和外圈放大到地球的大小,它们的表面偏差不会超过1米。

高铁轴承滚道的表面粗糙度要求在0.2微米以下。这相当于在1毫米的长度上,表面起伏的高度差不超过0.2微米,这种光滑度几乎接近镜面。这完全可以称的上高铁版的“水滴”了。
这些精密度要求确保了高铁轴承在极高速度和重载条件下依然能够保持平稳和可靠的性能。制造如此高精度的轴承,不仅需要顶尖的技术和设备,更需要在材料选择、加工工艺、质量控制等方面的严格把控。这也是为什么高铁轴承的自主生产成为了高铁国产化的最后一个重要难题之一。

高铁轴承的进口比例依然较高。根据相关统计数据,进口轴承在中国高铁轴承市场中的占比大约在70%左右。特别是在高端、高速和超高速列车上,进口轴承几乎占据了主导地位。
中国高铁所使用的轴承主要依赖于几家国际知名的轴承制造商。这些供应商拥有丰富的高铁轴承制造经验和先进的技术,能够提供符合高铁运行需求的高精度、高耐久性的轴承。

连接广州、深圳和香港的广深港高铁,是中国最繁忙的高铁线路之一。在这一项目中,使用的高速列车轴承同样依赖于日本和德国的进口产品。
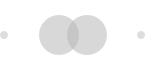
技术差距揭秘:中国为何难破 '轴承之困'?
正所谓基础不牢,地动山摇,中国的高铁轴承技术久久无法突破,这还是主要归因于起步晚。
中国的高铁技术起步较晚,真正大规模发展高铁是在2000年之后。相比之下,日本、德国等高铁技术发达国家早在20世纪70年代就开始研究和应用高速铁路技术。例如,日本的新干线在1964年就开始运营,德国的ICE列车也在1991年投入使用。

这些国家的轴承制造商,如日本的NSK、NTN,德国的舍弗勒和FAG,已经在高铁轴承技术领域积累了半个世纪的经验。而中国在高铁技术方面的积累时间相对较短,技术基础相对薄弱。
而这些先行者“捂着金碗不叫穷人吃饭”,长期以来对精密技术进行技术封锁。

即便中国已经掌握了大部分高铁技术,但在高铁轴承领域,国际技术封锁使得中国难以获取最先进的设计和制造技术。这种技术壁垒使得中国在高铁轴承领域难以实现快速突破。
中国高铁轴承革命:自主研发在路上
截至2020年,中国高铁总里程已超过3.7万公里,运营速度达到世界领先水平。但目前,只有速度低于140公里/小时的高铁轴承能够实现国产化,一旦速度超过这一限制,仍然依赖进口轴承。

甚至有外媒嘲讽到,中国高铁轴承100%依赖进口。这两年我国也在不断加大对轴承的研发力度,洛阳LYC轴承公司成功研制出了适用于时速250公里和时速350公里的高铁轴承,并经过了长达120万公里的耐久性测试。
其实,我国还具有生产轴承的天然优势,那就是我国是一个轴承钢生产大国。

而现在我国已经成功开发出一种新型高温不锈渗碳轴承钢,这种轴承钢具有高强韧性及耐温、耐蚀等良好综合性能。目前,不仅国内在使用这种新型材料,国外,包括我们刚才所提到的斯凯孚、舍弗勒等国际大公司也在疯狂的向我们申请订单。
当然,高铁轴承真正把我们难住的并非材料,而是真空脱气冶炼技术。有效去除了钢材中的氢、氧、氮等有害气体和非金属夹杂物。这种高纯净度的材料能够显著提升轴承的抗疲劳性能和耐久性。

虽无法和国际上最先进的技术媲美,但我国也在这一方面有一些突破。
我国研究团队创新性地提出了“节流过热+汽水换热”的方式,使蓄热器饱和蒸汽连续稳定地过热10~20℃,并可自动控制蒸汽的过热度。这项技术有效降低了能耗,提高了储氢合金性能。这项技术具有自主知识产权,已在多家企业得到推广应用。

现在我国的一些车型已经陆续换上了自主研发的轴承,中国在高铁轴承自主研发方面投入了大量资金和资源。随着技术积累和持续创新,预计未来5至10年内,国内企业将在高性能材料、精密加工和热处理等关键技术领域实现重大突破。
