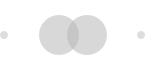
遭遇断供
华为被美国断供,最可怕的地方就是买不到高端芯片了。正常情况下华为已经是全球通讯产业老大,手机制造老二,登顶第一也就是一两年的事。如果没有芯片,所有高端电子产品都做不出来,企业现在面对的不是登顶世界第一问题,而是生存问题。

华为麒麟芯片
芯片制造不仅对华为重要,对整个高科技产业都是至关重要的,所有的技术最终都需要靠芯片来实现。我们国家在芯片制造上离领先水平还有不少差距,2019年我国进口产品最多的就是芯片,总价值达到了惊人的3000亿美元,甚至超过了我们一直最缺的东西 - 石油。
不仅对华为,欧美国家通过瓦森纳协议对我国高科技产业进行封锁,导致我们买不到最先进的制造设备。我们现在面临的困境是既不能生产,也不能进口。整个产业链的多个关键环节都被控制在欧美国家手中,研发要想全面突破还需要很多年。
当然其中最重要的就是生产芯片的光刻机,目前最先进的就是荷兰阿斯麦(ASML)的极紫外(EUV)光刻机,这台光刻机是全世界独一份,高端市场份额100%。华为想找代工厂用极紫外光刻机加工芯片,不行,中芯国际订购一台,对不起,不批准。

阿斯麦(ASML)极紫外(EUV)光刻机
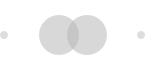
那么有没有可能突破封锁,来一次弯道超车?
光刻机,可能短时间无法突破,国产现状是上海微电子装备将于2021-2022年交付28纳米光刻机。距离最先进的制程还有3-4代差距。一些实验项目能够实现10纳米以内的线宽,但是离完整的设备还有很远的差距。

上海微电子装备的90纳米光刻机
最近一个令人振奋的消息就是,中国科学院院士、北京大学电子学系主任彭练矛教授和北京大学电子学系张志勇教授团队发展了全新的提纯和自组装方法,制备出了高密度高纯半导体阵列碳纳米管材料,并在此基础上实现了晶体管和电路。这一成果,将为碳基半导体进入规模工业化奠定基础,也为我国芯片制造产业实现“弯道超车”提供巨大潜力。

彭练矛教授和张志勇教授团队在Nature发文
正式的新闻稿提到了“弯道超车”,这到底意味着什么。
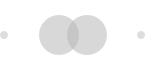
硅基芯片
我们首先看一下硅芯片是怎么回事。硅芯片简单说就是在硅片上制造出大量晶体管,目前最先进的芯片能够集成上百亿的晶体管。晶体管有两种类型,电子型和空穴型,向硅中掺杂不同的离子就可以制造出这两种晶体管。
光刻机的作用就像是雕刻一样,用光在硅片上雕刻出制造晶体管的源极、漏极和栅极,再用离子注入机给这些电极掺杂,就得到了晶体管。

进入21世纪以来,传统硅基芯片的发展速度日益缓慢,晶体管的特征尺寸 - 就是我们常说的14纳米、10纳米、7纳米等等 - 越来越小。到7纳米以下,已经无限接近硅基芯片的物理极限了,电极间漏电越来越严重,同一块芯片上的不同晶体管之间的稳定性越来越差,研发投入越来越高。
一方面是技术封锁,另一方面硅基半导体发展越来越慢,如果找到其他的制造方法,现在刚好是一个超车的好时机。科学家一直希望找到寻找能够替代硅的芯片材料,其中石墨烯和碳纳米管就是最有前景的方向之一。这两种东西都是纯碳,所以我们把以石墨烯或碳纳米管为基础的芯片叫做碳基芯片。
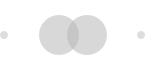
碳基芯片有什么优势,它能解决什么问题?
理想情况下,碳纳米管中电子平均自由程可以达到几微米,由于电子器件长度最多也就几百纳米,在这个范围内电子几乎可以不受阻碍地移动。

碳纳米管
通过控制碳纳米管的结构,可以得到金属管和半导体管。
典型的金属性碳纳米管在室温下电阻率为10^-8欧姆·米,性能优于最好的金属导体(银:1.59×10^-8欧姆·米)。
碳纳米管特殊的几何结构,决定了表面以及结构的缺陷对电子传输几乎没影响,而硅半导体必须要人为制造缺陷而且缺陷的影响是极大的。室温下,碳纳米管中电子和空穴的载流子迁移率,是最好的硅基半导体材料的1000倍。载流子迁移率越大,说明它移动效率越高,那么就可以把功耗做的越小,碳纳米管能够大大降低芯片的功耗。
碳纳米管器件不仅具有优异的电性能,其导热系数也达到了6000瓦/米·开尔文,远远优于最好的热导体,比如20℃时铜的导热系数是381瓦/米·开尔文。
另外,碳纳米管器件还能承受极高的电流上限,有非常好的高频响应。
总之,碳纳米管的主要优势在于它拥有完美的结构、超薄的导电通道、极高的载流子迁移率和稳定性,一旦制成芯片,性能将优于所有已知的其他半导体材料。
硅要实现电子型和空穴型半导体,就需要对硅进行掺杂,在硅芯片生产用到离子注入机就是做这个的。而用碳纳米管则不需要,采用金属铅作为接触电极,半导体为空穴型;采用金属钪或者钇作为接触电极,半导体为电子型。
因此,通过化学掺杂来控制材料电学性质,具体说就是用光刻机刻蚀出电极形状,然后再用离子注入机掺杂,这是传统半导体工艺中最关键也是最复杂的步骤,被碳基半导体彻底抛弃了。采用“无掺杂”方式不仅能够实现高性能的电子器件,而且能够减少一半的生产流程。
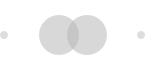
碳纳米管晶体管
2017年1月,彭练矛团队研制出高性能5纳米栅长碳纳米管CMOS器件,这是世界上目前能做出的最小的高性能晶体管,综合性能领先目前最好的硅基晶体管十倍,接近了理论极限。其工作频率是英特尔最先进的14纳米商用硅晶体管的3倍,能耗却只有的1/4。

5纳米栅长碳纳米管晶体管
功耗也是目前硅基集成电路发展瓶颈之一,彭练矛团队进一步提出并制备了一种新型超低功耗晶体管 - 狄拉克源晶体管,可大幅降低晶体管的驱动电压,这很有可能成为3纳米及以下技术节点的解决方案。

狄拉克源晶体管
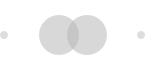
碳基芯片
晶体管做出来了,下一步就是在基板上规模化制造了。当然还面临许多的挑战。比如说需要解决的是半导体碳纳米管的纯度控制,以及碳纳米管阵列的有规则排列和密度控制。
制造出半导体特性的碳纳米管是一个重要挑战。碳纳米管相当于把石墨烯卷成筒状,根据对齐的方式不同,碳纳米管就会表现出不同的特性,有些是金属性质的,有些是半导体性质的。但是如果要做芯片,我们希望碳纳米管全部是半导体性质的。

不同形式的碳纳米管
彭练矛院士的方法是从现有的碳纳米管中筛选出具有半导体特性的来。
首先从市场上购买的碳纳米管开始,这些碳纳米管即包含金属性质的也包含半导体性质的,把它们放置在甲苯中,溶液中添加一种特殊的聚合物,聚合物会包裹着碳纳米管。然后把溶液放入离心机进行离心操作,这样可以对碳纳米管进行筛选,重复两次以上就可以获得99.9999%以上的半导体碳纳米管。其他的方法目前只能达到的99.99%,新方法把纯度提高了两个数量级。
张志勇教授介绍说,对于极大规模的高端集成电路来说,还需要把纯度再提升2-3个数量级。而多次重复离心操作,可以进一步提升纯度。当然也需要解决一些辅助工艺问题。
下一步需要把碳纳米管按照设计要求精确的排列好。
研究人员在硅片表面涂上一层聚合物薄层,再把硅片浸入碳纳米管溶液中。碳纳米管的聚合物涂层遇到硅片的聚合物涂层,两者之间形成氢键,这就好像是碳纳米管按特定顺序“粘”在硅片上。然后再把硅片从溶液中缓慢拉出,碳纳米管就会一根接着一根的沿着水平方向自动平行排列。

碳纳米管密排工艺
最终,团队在10厘米基底上制备了密度高达120排/微米、半导体纯度99.99995%、直径分布1.45±0.23纳米的碳纳米管平行阵列。实际上在实验室中已经可以在直径20厘米的硅片上做到了。

密度达到100-200/微米、半导体纯度超过99.9999%的碳纳米管平行阵列
研究人员现在已经可以在基板上批量制备100纳米栅长的碳基场效应晶体管和五阶环形振荡器电路,成品率超过了50%,最高振荡频率达到8.06GHz,且首次超越相似尺寸的硅基器件和电路。

碳纳米管高速集成电路
北京大学团体已经建立了一条10厘米晶圆的生产线,可以说是在规模化生产上迈出了非常重要的第一步。团队的下一个目标,是在2-3年内完成90纳米碳基芯片工艺开发,性能上相当于28纳米硅基器件。虽然不是高端技术水平,但已经达到进入市场的门槛。再往后,采用28纳米工艺的碳基芯片则可以实现等同于7纳米技术节点的硅基芯片,这基本相当于目前市场上最高制程水平的芯片。
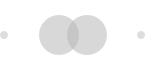
来自美国的竞争
国外目前也在努力研究,6月1日,麻省理工学院(MIT)展示了在200毫米的标准晶圆上批量制造的碳纳米管场效应晶体管。这个技术略有不同,它是通过沉积法让碳纳米管边对边地在晶圆上生长,制成了14400×14400的场效应晶体管阵列。

MIT的研究成果
MIT团队在两个不同的工厂成功地测试了这种新方法,分别是 Analog Devices(ADI)和SkyWater Technology的半导体代工厂。这两家工厂都是纯粹的硅基半导体加工厂。SkyWater工厂的常规制程是130、90和65纳米,还是比较落后的。

SkyWater工厂
这次MIT的研究仅仅是制造工艺的演示,而且晶体管的栅极长度(即制程)为130纳米,碳纳米管生长工艺也只实现了45排/微米。
但是,有一点非常重要,MIT的这次尝试证实了碳基芯片可以在传统的硅基芯片加工厂生产,这简化了许多步骤,而且对于工艺制程要求很低。
规模化生产,即使是某些工艺用到光刻机,也不需要最先进的极紫外光刻机,达到目前顶级水平28纳米光刻机基本够用。有消息说国产正在研发的光刻机即将达到11纳米的水平,光刻机的难题很可能通过碳基芯片绕过去。
而且,这个说法实际上非常保守,前面提到的SkyWater,正全力转向碳基芯片,他们宣称使用90纳米制程能够达到7纳米硅基芯片性能,具有50倍的速度优势。虽然技术比我们落后,但是画饼水平还是很强大的。
彭练矛院士团队的成果目前有2年的领先优势,美国人一时半会还是追不上的。
实验室技术已经在原理、材料、小规模生产上实现了突破。目前最缺的,就是需要芯片加工厂的合作,在真正的大规模生产工艺上进行突破和优化。
如果一切顺利,3-5年实现28纳米制程,5~10年实现10纳米制程,那个时候有没有荷兰光刻机都不重要了,我们将有机会站在世界之巅。